激光打孔与化学蚀刻结合技术:微孔加工的新方向
激光打孔与化学蚀刻结合技术:微孔加工的新方向
引言
随着制造业的快速发展,微孔加工技术在多个领域展现出了巨大的应用潜力。特别是在精密仪器、电子产品、航空航天以及生物医学等领域,对微孔的尺寸、形状和精度要求日益提高。传统的加工方法往往难以满足这些高要求,而激光打孔与化学蚀刻作为两种先进的加工技术,各自具有独特的优势。本文旨在探讨激光打孔与化学蚀刻结合技术在微孔加工领域的新方向,分析其在提高加工精度、效率及环保性方面的作用。
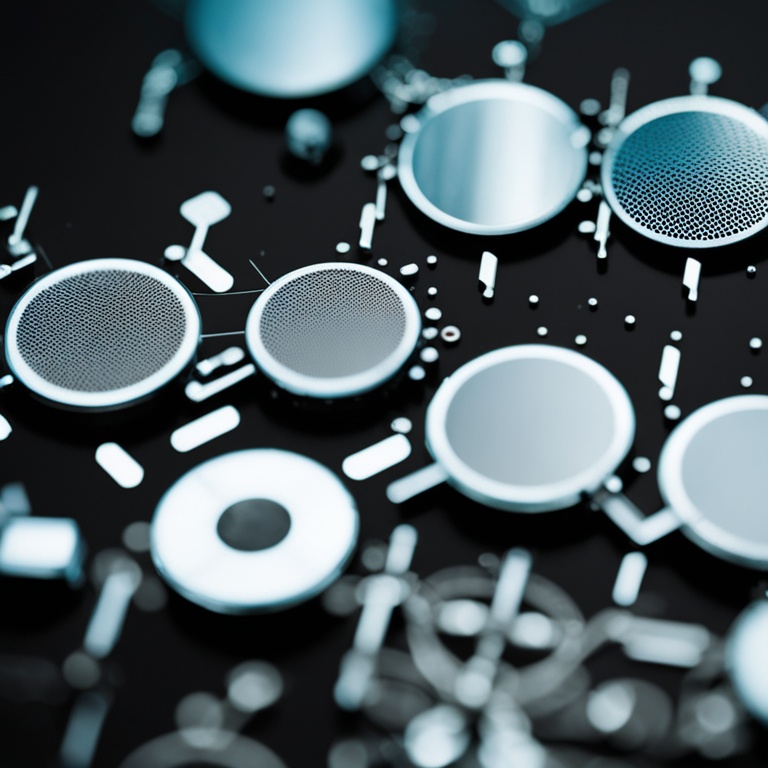
激光打孔技术的优势
激光打孔技术以其高精度、高效率、通用性强等特点,在现代制造领域占据重要地位。该技术利用高能量激光束聚焦后产生的高温使材料局部熔化或气化,从而实现打孔。激光打孔的孔径精度可达到微米级,且孔洞边缘光滑,无毛刺,特别适用于加工硬质材料和高熔点材料。
在0.1mm以内的微孔加工中,激光打孔技术展现出了卓越的性能。其加工速度快,可实现高效率的群孔加工;同时,激光打孔为非接触式加工,避免了机械钻孔易断钻头的问题,降低了工具损耗和加工成本。
化学蚀刻技术的特点
化学蚀刻技术则是通过化学反应或物理撞击作用移除材料的一种加工方法。其中,光化学蚀刻是应用最为广泛的一种,它通过曝光制版、显影后,将要蚀刻区域的保护膜去除,再接触化学溶液进行溶解腐蚀,形成凹凸或镂空成型的效果。化学蚀刻技术成本低廉,适用于大批量生产,且对材料的要求相对较低,能够加工出复杂的图形和图案。
然而,传统的化学蚀刻技术也存在一些局限性,如精度相对较低、加工深度有限,且可能产生环境污染。但随着工艺设备的不断改良和环保技术的引入,这些问题正在逐步得到解决。
激光打孔与化学蚀刻结合技术的优势
将激光打孔与化学蚀刻技术相结合,可以充分发挥两者的优势,实现微孔加工的新突破。具体来说,这种结合技术具有以下优势:
1.提高加工精度:激光打孔技术的高精度特点可以为化学蚀刻提供精确的加工边界,减少蚀刻过程中的偏差,从而提高整体加工精度。
2.优化加工效率:激光打孔技术的高效率特点可以缩短加工周期,而化学蚀刻技术则适用于大面积的加工。两者结合可以实现快速且高效的微孔加工。
3.降低成本:虽然激光打孔设备的初期投入较高,但其高效、高精度的特点可以降低废品率和返工率,从而间接降低生产成本。同时,化学蚀刻技术本身成本低廉,适用于大批量生产,进一步降低了整体加工成本。
4.环保性好:随着环保意识的提高,制造业对加工技术的环保性要求也越来越高。通过优化化学蚀刻工艺和引入污水处理循环体系,可以将环境污染降至最低。
应用场景与案例分析
激光打孔与化学蚀刻结合技术在多个领域具有广泛的应用前景。例如,在精密仪器制造中,该技术可以加工出高精度的微孔,满足精密测量和控制的需求;在电子产品制造中,该技术可以加工出复杂的电路板和元件孔,提高产品的性能和可靠性;在航空航天领域,该技术可以加工出轻质高强度的复合材料构件,减轻飞行器重量,提高飞行效率。
以某航空发动机叶片的微孔加工为例,传统加工方法难以在叶片表面加工出高精度、高质量的微孔。而采用激光打孔与化学蚀刻结合技术,首先利用激光打孔技术在叶片表面形成精确的孔洞边界,然后利用化学蚀刻技术进行深度加工和表面处理,最终实现了高精度、高质量的微孔加工,大大提高了叶片的性能和寿命。
未来发展方向
随着科技的进步和制造业的发展,激光打孔与化学蚀刻结合技术将在微孔加工领域发挥更大的作用。未来,该技术将朝着以下几个方向发展:
1.提高加工精度和效率:通过不断优化激光打孔和化学蚀刻的工艺参数和设备性能,进一步提高加工精度和效率。
2.降低成本和环保性:引入更先进的环保技术和设备,降低加工过程中的环境污染和能源消耗;同时,通过优化生产流程和材料利用率,降低生产成本。
3.拓展应用领域:随着制造业的多元化发展,激光打孔与化学蚀刻结合技术将不断拓展新的应用领域,满足更多行业对高精度、高质量微孔加工的需求。
结论
激光打孔与化学蚀刻结合技术作为微孔加工领域的新方向,具有高精度、高效率、低成本和环保性好等优势。该技术的出现不仅推动了制造业的发展,也为精密仪器、电子产品、航空航天等多个领域提供了高效、精准的加工解决方案。未来,随着技术的不断进步和应用领域的不断拓展,激光打孔与化学蚀刻结合技术将在微孔加工领域发挥更加重要的作用。
本文版权归网站所有,转载请联系并注明出处:
http://www.yiylaser.com/article-detail/BvXRpexW