激光打微孔工艺对材料表面质量的影响研究
激光打微孔工艺对材料表面质量的影响研究
引言
随着现代制造业的快速发展,高精度、高质量的微孔加工技术在航空航天、电子器件、生物医学等多个领域展现出巨大潜力。激光打微孔工艺因其非接触、高精度、高效率等优点,成为微孔加工领域的重要技术手段。本文旨在探讨激光打微孔工艺对材料表面质量的影响,分析不同加工参数下材料表面粗糙度、硬度及残余应力的变化规律。
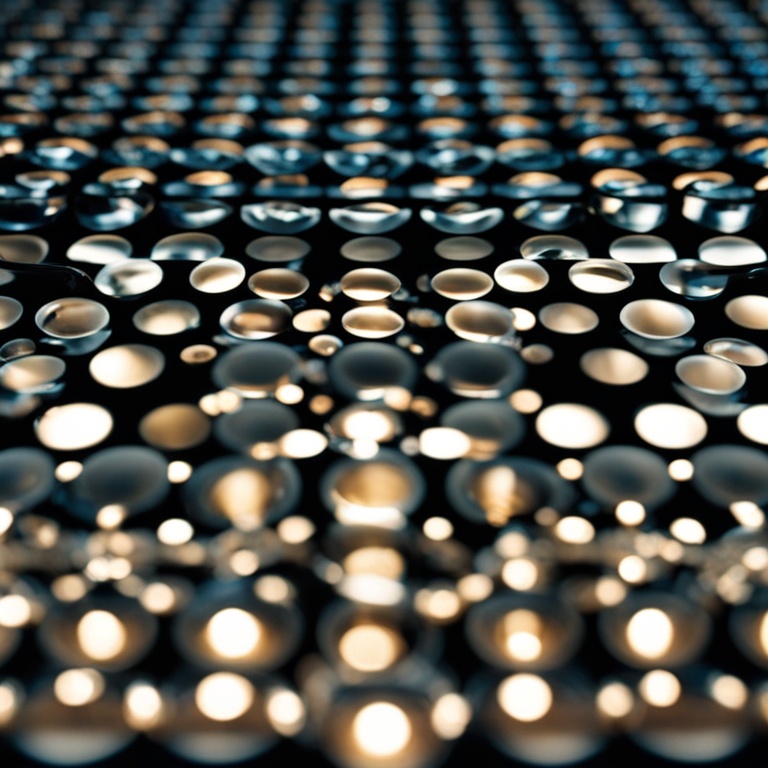
激光打微孔工艺概述
激光打微孔工艺是利用高能量密度的激光束照射材料表面,通过局部熔化、汽化或热应力等作用机制,实现微小孔洞的加工。激光加工过程中,激光束的脉冲能量、脉冲宽度、脉冲重复频率、扫描速度及离焦量等参数均对加工效果产生显著影响。飞秒激光作为激光技术的重要分支,以其极短的脉冲宽度和极高的峰值功率,在微孔加工领域展现出独特的优势。
激光打微孔对材料表面粗糙度的影响
表面粗糙度是衡量材料表面质量的重要指标之一。激光打微孔过程中,激光束与材料表面的相互作用会导致表面微观形貌的改变。通过调节激光功率、扫描速度等参数,可以有效控制加工区域的热输入量,进而影响表面粗糙度。
实验表明,当激光功率较低、扫描速度较快时,激光束对材料表面的热影响较小,形成的微孔边缘较为平滑,表面粗糙度较低。反之,高功率、低速度的加工条件则容易导致材料表面过热,产生熔渣、飞溅等现象,增加表面粗糙度。此外,合理的离焦量设置也能在一定程度上改善表面粗糙度。
激光打微孔对材料表面硬度的影响
激光加工过程中,材料表面会受到激光束的瞬时加热和快速冷却作用,导致表面组织发生相变和重结晶,进而影响材料表面硬度。
研究表明,激光打微孔后,材料表面往往形成一层淬火层,该层组织致密、晶粒细小,具有较高的硬度和耐磨性。通过优化激光加工参数,如提高激光功率密度、缩短脉冲宽度等,可以进一步增强淬火层的硬度和性能。然而,过高的激光能量也可能导致材料表面出现裂纹、重铸层等缺陷,降低表面质量。
激光打微孔对材料表面残余应力的影响
残余应力是激光加工过程中不可避免的现象之一。激光束对材料表面的快速加热和冷却会导致热应力的产生和积累,进而形成残余应力。
合理的激光加工参数选择可以减小残余应力的产生。例如,通过降低激光功率密度、增加脉冲宽度等方式,可以减缓材料表面的加热速率和冷却速率,从而降低残余应力水平。此外,采用多脉冲加工、预热处理等辅助手段也能有效改善残余应力的分布状况。
飞秒激光在微孔加工中的独特优势
飞秒激光以其极短的脉冲宽度和极高的峰值功率,在微孔加工领域展现出独特的优势。相比传统纳秒、皮秒激光,飞秒激光加工过程中热影响区更小,加工精度更高,能够显著减少重铸层和微裂纹的产生。
在航空发动机涡轮叶片等高精度部件的加工中,飞秒激光微孔加工技术能够确保冷却孔的质量和精度满足严苛的工业标准。通过优化飞秒激光的加工参数和工艺方法,可以实现对微孔尺寸、形状及表面质量的精确控制。
结论与展望
激光打微孔工艺对材料表面质量具有显著影响。通过合理调节激光加工参数,可以有效控制材料表面粗糙度、硬度和残余应力等关键因素,提高微孔加工的质量和精度。飞秒激光作为激光加工技术的前沿领域,其在微孔加工中的独特优势为高精度、高质量微孔加工提供了有力支持。
未来,随着激光技术的不断进步和应用领域的不断拓展,激光打微孔工艺将在更多领域发挥重要作用。同时,对激光加工过程中材料表面质量变化机制的深入研究也将为激光加工技术的发展提供更为坚实的理论基础和技术支撑。
本文版权归网站所有,转载请联系并注明出处:
http://www.yiylaser.com/article-detail/Wl6avL4B